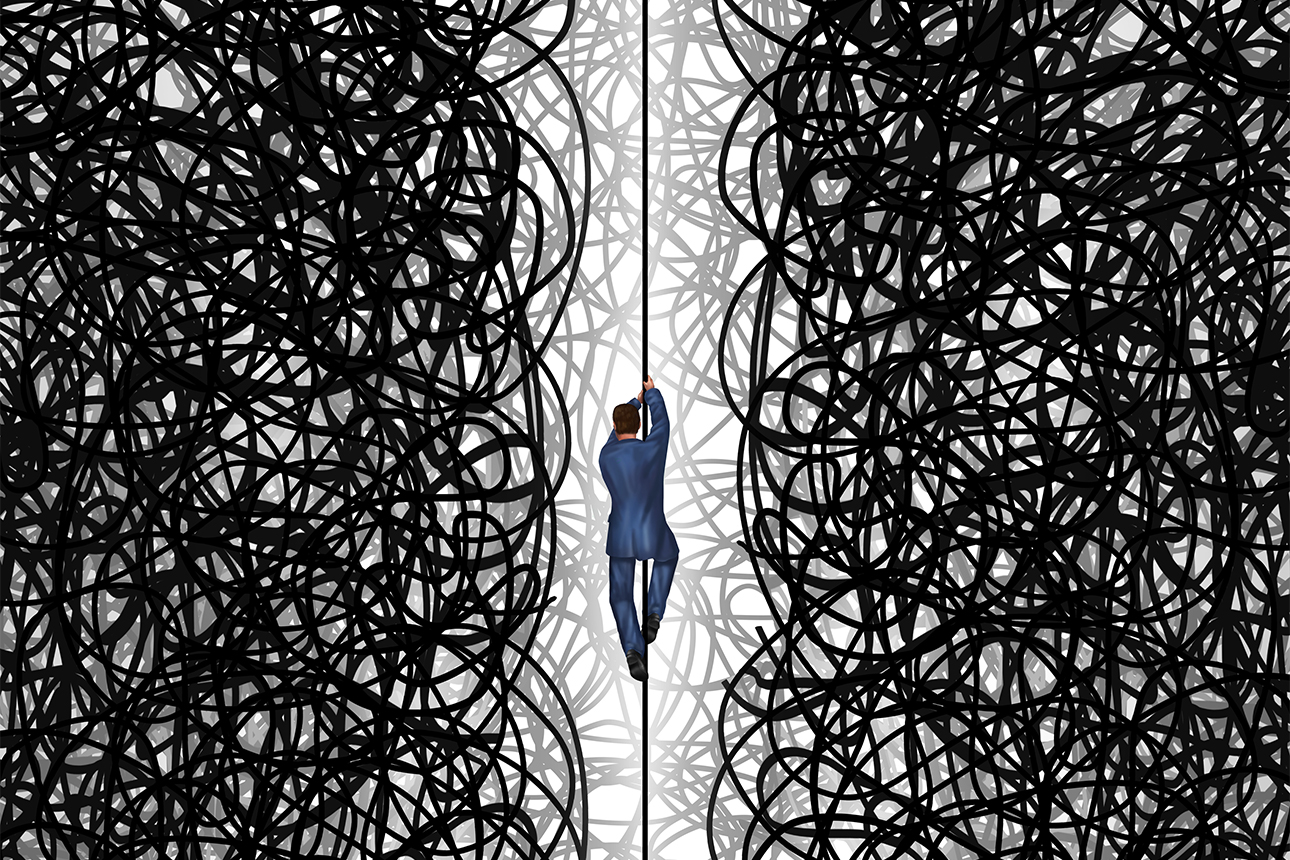
The outbreak of COVID-19 has exposed the fragility of the global supply chain and, in turn, many companies’ organizational structures. In their pursuit to become ever more efficient, bear fewer costs, and eliminate redundancies, many organizations have come to rely on tightly coupled, interdependent systems. In this type of system, there is little slack and few buffers among its parts and, as we are seeing now, little room to maneuver when something goes seriously awry. Dependencies span vast geographic distances, and they can be especially vulnerable to delays in another part of the chain.
In the auto industry, for instance, manufacturers — from Toyota in Japan to General Motors in the U.S. — all rely on parts from China, and the industrywide emphasis on just-in-time delivery means they don’t carry much safety stock. In normal circumstances, this system is fiercely efficient and productive, but no one can build a car with only 99% of its parts. Indeed, when Hyundai first shuttered its assembly plants in South Korea in February, it was not because of the rampant spread of COVID-19 in the country, but because the company couldn’t keep its plants open without Chinese parts. In an inflexible system populated with companies run from the top down that are too slow to adapt, those channels that prove so efficient in periods of calm are now a source of severe disruption.
Organizational rigidness has exacerbated supply chain issues across a number of sectors in recent weeks and in a wide range of companies, including Apple, Toyota, and Hasbro. But this impact has not been universal.
While most manufacturers in China were only just beginning to restart production at the end of February, Haier Group — one of the world’s biggest home appliance manufacturers — already had its factories operating at full capacity again, thanks in large part to the company’s distinctive organizational design. For years, Qingdao-based Haier has organized itself not as a top-down pyramid but as a swarm of self-managing business units that can make their own rapid adjustments to stay afloat in times of crisis.
The organizational reconfiguration that prepared Haier for the shock of coronavirus was several years in the making. Haier CEO Zhang Ruimin has always been obsessed with breaking the bureaucracy, and he is famous for saying “successful companies move with the times.” Around 2012, he issued midlevel managers an ultimatum: Choose to either be fired or become independent entrepreneurs. It was “the hardest decision” the CEO had ever made, but it was meant to transform the company from a few monolithic businesses into some 4,000 microenterprises, or MEs, most comprising just 10 to 15 employees. Early estimates indicate that Haier reduced its workforce by around 45% compared with its peak size, but it created new positions for more than 1.6 million.
What followed, for those who stayed, was an increase in autonomy. Zhang gave the leaders of each ME the suite of decision-making powers — the power to hire staff or to control distribution — that would ordinarily be granted to the CEO of a company, not to a division leader. Instead of being centrally orchestrated, these MEs independently transacted with one another and were given full autonomy to deliver the final product to consumers. Certain MEs manufacture specific component parts, while others provide services like HR or design. Haier also introduced several internal platforms to facilitate transactions among MEs, likening the idea to an app store. It enabled coordination but did not direct it.
During the coronavirus outbreak, Haier’s microenterprises have buoyed the business. With the freedom to adjust their own supply chains according to specialized knowledge and up-to-date information, MEs have shifted their dependencies ever so slightly. Because each ME was able to act rapidly to reduce disruption, the company as a whole was able to recover more quickly than its competitors. With supplier resources spanning the Americas, Southeast Asia, South Asia, and Europe, Haier fulfilled 99.8% of orders throughout February, with 60% of products manufactured in factories outside of China.
Though a full-scale organizational transformation like Haier’s simply isn’t possible overnight, there are a few steps companies can take to crisis-proof their org charts — and bottom lines — in the short term.
- Democratize the decision-making process at the cross-functional level. In the face of this crisis, although it may not be possible for companies to increase the autonomy of specific product departments or locations, it is possible to temporarily allow cross-functional teams to have more decision-making power. Think of these as “flying SWAT teams,” with limited requirements to report back up the hierarchy. Increasing autonomy, even on a provisional basis, is often scary, but a guiding principle should be that your employees on the ground are an asset for making tough calls — in other words, trust your teams’ capabilities and skills.
- Embrace single-threaded leadership. Single-threaded leadership is well known for its success in tech giants such as Amazon and refers to giving a leader a single problem to solve with a specific budget and timeline. Taking a cue from the venture capital world, this form of leadership entails companies identifying a startup idea with potential and handing it to one leader to bring it to life within the organization. Within this clearly defined role, leaders are able to maximize focus and minimize distractions where possible — at least for the time being.
- Communicate clearly and transparently. Leaders will need to make use of digital workflows and start recording who decides what and why. When possible, record business meetings on video and make them available to everyone in the organization via a simple internal communications platform. This model provides transparency into the key information employees need, thus increasing trust, and it provides clarity around decision-making (and responsibilities and accountability) at the top while lowering communication costs.
- Prioritize a small set of digital collaboration tools. Often, internal communication is hindered by legacy systems and situations such as waiting for a decision in “next week’s meeting.” In order to aid crisis management, companies should select one set of digital collaboration tools and go all-in. There are plenty of tools around that can be easily installed and used for virtual meetings, instant communication, and project work collaboration. Whether it is Zoom or Skype or Slack, the Indian platform Flock, or the Chinese app DingTalk, it needs to meet only one criterion: ease of use. It should take no more than 48 hours to implement.
Speaking of crises and how they can expose weak companies, Warren Buffett once said that “only when the tide goes out do you find out who is not wearing a bathing suit.” The COVID-19 pandemic has exposed the fallacy of our singular pursuit of efficiency. But it also provides organizations the opportunity and impetus to end corporate bureaucracy.
How Autonomy Creates Resilience in the Face of Crisis
No comments:
Post a Comment